Why Have a Quality Control Strategy?
Having a system that ensures quality is an obligation for all companies, regardless of the industry they belong to. The advantages it offers are more than convincing. We review the truly indisputable ones.
- Reduction of defect rates in products. Furthermore, in case they occur, it is easier to detect them before they reach the final customer.
- Reduction of costs: with fewer failures, economic losses due to waste are minimized. Additionally, you will invest fewer resources in fixing the causes of these defects.
- Increase in profits as a result of higher productivity.
- You avoid production delays.
- Waste will be reduced, making you more environmentally friendly.
- Avoid legal issues: a defective product can lead to lawsuits that are very damaging to the company. Think, for example, of the food industry and the food poisoning related to its products.
- Improvement of the corporate image with current and potential customers, as well as the general public.
- Improved risk management: quality is also closely related to the safety of factory employees. An aspect that has gained even more importance with the current health situation.
- Optimal document management: having the quality control in a company implies a significant amount of various types of documents. Therefore, companies must organize them optimally.
- Improvement of production processes and logistics: quality affects all stages of the production process, including aspects related to warehouse management and the transportation of products and raw materials.
What is the role of the quality control department?
For all these benefits to become a reality, there must be a body responsible for planning and coordinating all actions involved in business quality management. That is why the vast majority of companies have quality control departments. What are their main functions?
First, we can talk about defining the company’s quality policy. This is nothing more (or less) than a document that outlines the company’s commitment to quality, as well as to its customers and continuous improvement. Additionally, the quality policy must be consistent with the company’s mission, vision, and values.
The quality department must take the lead in all quality-related actions, such as:
- Risk assessment.
- Creation and monitoring of procedures for quality control.
- Planning and conducting audits, both internal and external.
- Development of corrective actions.
- Management of all involved documents.
Regarding human resources, the quality control department must promote communication and the exchange of information among the different teams involved. Additionally, it must ensure that all employees receive the appropriate training tailored to their responsibilities.
What does the quality control plan contain?
Carrying out all these quality measures effectively requires a perfectly functioning system. And all of this must be outlined in a document known as the quality control plan.
This plan specifies the procedures to be carried out, the resources available, when the proposed actions should be implemented, and who will be responsible for each of them.
The main points included in a quality control plan are:
- What are the quality objectives to be met? What specifications must your product comply with?
- What procedures must be carried out to achieve this, and what phases does it consist of?
- What responsibilities does each person involved in quality control have?
- What do quality tests and audits consist of, when are they carried out, and who is responsible for them?
- How the results will be handled.
Why do you need to digitalize quality control?
As you can see, managing quality effectively in a company is not exactly a piece of cake. It requires maximum commitment from all parties, continuous data collection and processing, as well as interpretation and effective decision-making.
To make this task easier, we recommend using digital tools that will make it much more manageable. These tools are based on:
- The sensorization of the plant, so that it collects real-time data on the key variables of the manufacturing process.
- The interpretation of this data with Big Data and Artificial Intelligence systems.
- The representation of this interpretation through dashboards that are easy to visualize and understand.
- The digitalization of documents, creating a paperless environment that is proof against loss, confusion, malicious actions, and more easily accessible for everyone.
- Improved planning of quality audits.
- The conduct of these audits, which includes the direct input of all their results and corresponding evidence into a digital system.
- The management of corrective actions.
- The possibility of including alternatives that result in greater involvement from all staff. For example, through the gamification.
- The ability to track all activity, strengthening the traceability of processes.
- Strengthen the health safety of everyone. If we know the contacts a sick worker has had, we can prevent a complete halt in activity and ensure the health of their colleagues.
Without proper quality control guidelines, a company will have a very bleak future. Having them is not an option, and to make their implementation easier, you have attractive digitalization options at your disposal.
On our part, we can study your case and offer the solutions that best suit your business. We also have products that make it easier to carry out quality audits according to the Lean methodology of the 5S. Contact us and start giving a fresh approach to quality in your environment. We look forward to hearing from you!
Do you want to know what we do and how we do it? Visit our success stories and ask us anything you need to know.
KNOWLEDGE / Downloadables
Free eBook
OEE Efficiency
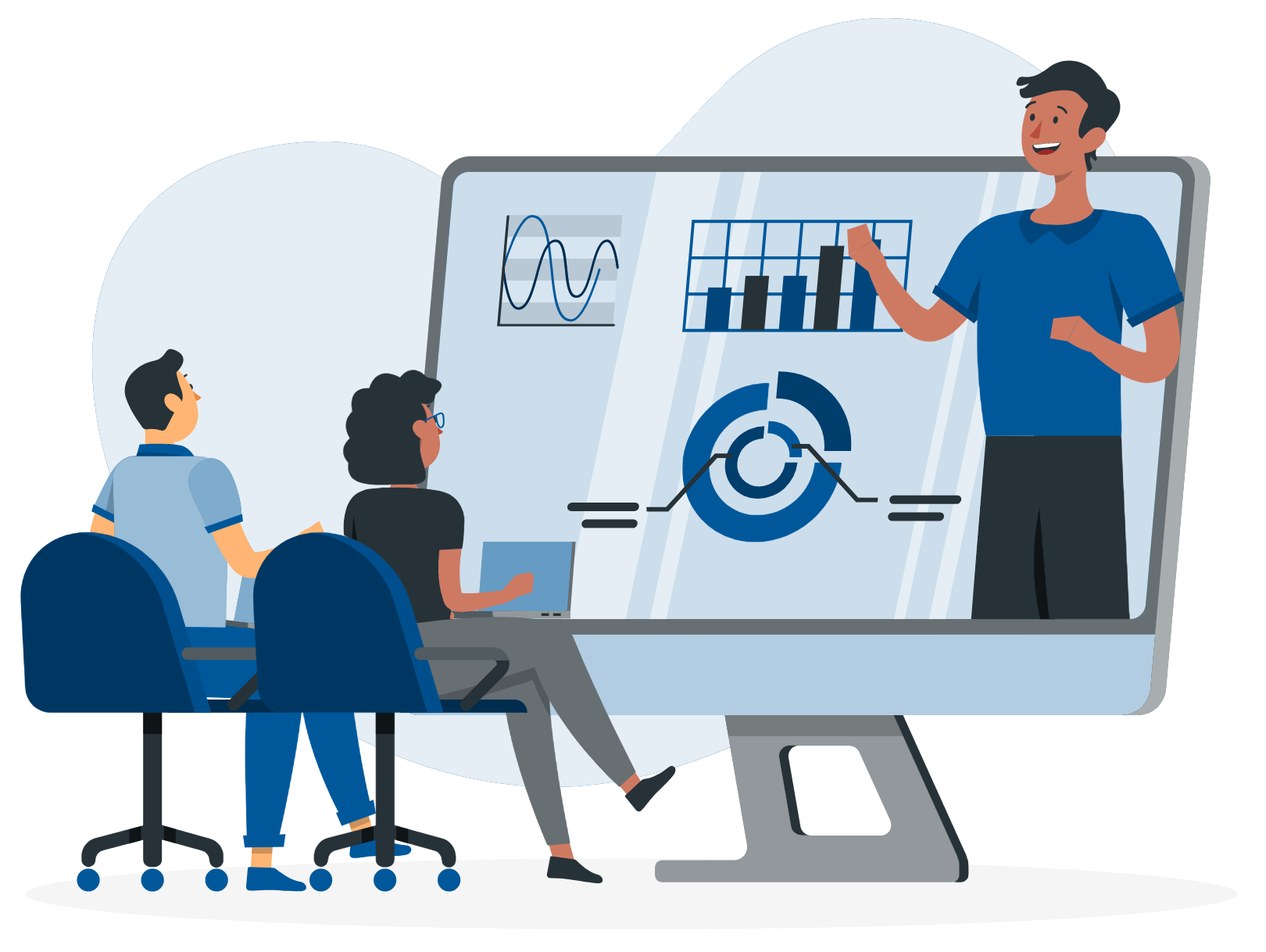
Discover the details of the OEE indicator, how to automate its calculation and the requirements your production processes must meet to implement it.