La filosofía y los principios de Lean Manufacturing abarcan un amplio espectro de técnicas que tienen como objetivo tirar a la basura todo lo que suponga un desperdicio desde el punto de vista de la productividad.
Para cumplir a la perfección con esta tarea de “basureros industriales”, las estrategias definidas por las 5S y Poka Yoke aportan pautas y medidas que dejarán tu fábrica impecable y rebosando eficiencia.
Así que si, como buenos industriales, os obsesiona el orden y hacer las cosas simples y que funcionen lo mejor posible, deberíais echarle un vistazo a las bases de las 5S y Poka Yoke. ¿Os animáis?
¿Qué son las 5S en la industria?
Si queremos conocer los orígenes de 5S, debemos remontarnos a 1960 y viajar a la compañía japonesa Toyota. Fue entonces cuando Sakichi y Kiichiro Toyoda, así como el ingeniero Taiichi Ohno, buscaron una alternativa a la cadena de montaje de Henry Ford.
La finalidad de la metodología de las 5S no es otra que eliminar lo superfluo, aquello que no aporta nada al proceso de fabricación, tanto en lo material como en los comportamientos de los implicados en cada etapa del mismo.
Entre estos elementos a eliminar podemos destacar el desorden y la suciedad, los movimientos innecesarios, los riesgos físicos para los trabajadores o la carencia de estándares que establezcan claramente pautas de trabajo, entre otros.
¿Cómo implantar las 5S?
El primer paso para arrancar la implementación de un sistema 5S en la industria será analizar al detalle los diferentes puestos de trabajo, procedimientos y flujos asociados.
Entre estas fases de la fabricación, algunas de las más comunes son los tiempos incurridos; los puntos de bloqueo físico, como los pasillos; la organización, autonomía y destrezas de los trabajadores; aspectos ergonómicos y de seguridad; cuellos de botella y aspectos logísticos y de calidad industrial.
Partiendo de este conocimiento en profundidad sabremos exactamente cómo actuar, definiendo objetivos alcanzables y medibles a corto plazo, de forma que las mejoras se aprecien claramente.
Consideraciones previas
Una de las primeras dudas que os vendrán a la cabeza será la de si se debe implantar 5S en toda la fábrica o si hacerlo paulatinamente por áreas.
Lo más aconsejable es la segunda opción, delimitando una zona o fase de la fabricación en la que experimentar, medir y aprender progresivamente de los errores cometidos para, posteriormente, aplicar esta sabiduría al resto de la planta.
Y ahora, es momento de abordar los 5 pasos fundamentales que son los que le dan nombre a la metodología.
1.- Seiri
Con Seiri se busca quitar de enmedio lo que no necesitamos para realizar nuestro trabajo. Ejemplo de estos elementos sobrantes son objetos que dificultan la maniobrabilidad, movimientos de materiales y personas innecesarios, exceso de stock e inventario y herramientas inútiles.
Gracias a Seiri conseguimos espacios más diáfanos y cómodos, mayor organización, eficiencia y seguridad laboral.
2.- Seiton
Una vez eliminado lo que no nos sirve, es hora de ordenar aquello que sí aporta a la fabricación. De esta forma ahorraremos tiempo a la hora de buscar lo que necesitemos en cada momento.
A través de Seiton averiguaremos cuál es la mejor situación de los útiles de trabajo mediante un estudio de su frecuencia de uso, en qué zonas se utilizan y su facilidad de manejo como variables más destacadas. Por supuesto, todo debe quedar debidamente documentado para su consulta rápida.
3.- Seiso
En esta etapa de las 5S se busca estar un paso por delante en lo que a fallos y defectos se refiere, de manera que podamos preverlos y tomar medidas de mantenimiento predictivo al respecto.
Para hacer efectivo este paso, la limpieza se convierte en el arma básica, de manera que gracias a ella, la maquinaria estará mejor conservada y se podrán hallar con más facilidad posibles deficiencias en ella.
Con todo ello conseguiremos reducir las averías y aumentar la productividad, así como la seguridad.
4.- Seiketsu
Una vez asentadas todas las medidas descritas en las anteriores S, es fundamental estandarizarlas y documentarlas por vías como pueden ser las guías técnicas.
Eso sí, estas guías deben redactarse de la forma más sencilla y esquemática posible, de manera que las personas que las consulten, puedan encontrar lo que buscan e interpretarlo sin dificultad ni demora de tiempo.
5.- Shitsuke
Por último, habrá que crear hábitos y medidas de disciplina para automatizar todo lo descrito anteriormente.
Finalmente, deberemos auditar periódicamente todos estos pasos, con una medición continua de los indicadores más relevantes. Una evaluación que permitirá describir acciones destinadas a la mejora continua.
Poka Yoke y la minimización de errores
Los errores son el principal lastre de cualquier proceso industrial. Por ello, su eliminación y, lo que es mejor, una prevención que impida la aparición de estos fallos. harán ganar varios puntos en lo que a eficiencia y productividad se refiere.
Aquí es donde tiene bastante que decir Poka Yoke. Este método englobado en Lean Manufacturing se centra en la detección, prevención y eliminación de estos defectos en las tareas de producción.
Poka Yoke hace especial hincapié en aquellos procesos que son más tendentes al fallo, como son las tareas repetitivas y tediosas de una línea de producción.
Para materializar Poka Yoke es habitual echar mano de sencillas formas y colores que faciliten al operario la interpretación de todas las órdenes a ejecutar. De esta forma se consigue ver de forma muy clara que se ha cometido un error en el trabajo. Por ejemplo, un dispositivo USB solamente puede conectarse en una orientación determinada o algunos softwares no permiten avanzar si se dejan algunos formularios en blanco.
Actualmente, los dispositivos Poka Yoke más en boga son aquellos consistentes en sistemas de detección y de alarma, normalmente visual y/o sonora que haga que el trabajador se dé cuenta al instante del error que ha cometido, donde los sensores tienen mucho que aportar.
Soluciones para aplicar 5S y Poka Yoke en la industria
Polaris proporciona todas las funcionalidades necesarias para implantar y monitorizar todos los aspectos relacionados con 5S y Poka Yoke en una planta industrial.
Mediante su módulo de Housekeeping podemos optimizar los procesos de auditoría que tienen como fin evaluar todas las características de estas metodologías Lean. Siendo de gran utilidad tanto para la parte auditada, como para la auditora.
Desde el punto de vista del auditor, se pueden redactar medidas correctoras de una manera ágil e intuitiva gracias a la disponibilidad de información en tiempo real.
Si nos ponemos en la piel del auditado, este obtendrá notificaciones inmediatamente después de que se hayan establecidos dichas medidas correctoras, de forma que podrá trabajar en ellas inmediatamente.
Además, gracias a la herramienta visual Kanban disponible, se puede observar la situación general de una forma sencilla e intuitiva.
Para finalizar, esperamos que, además de haber aprendido un poco de japonés (porque nunca se sabe), hayáis disfrutado adquiriendo nociones sencillas, pero muy prácticas, que pueden llevar a una planta industrial a un peldaño superior en cuanto a calidad y eficacia. ¡Gracias por estar ahí!
¿Quieres conocer qué hacemos y el modo en que lo hacemos? Visita nuestros casos de éxito y pregúntanos todo lo que necesites saber.
CONOCIMIENTO / Descargables
EBook gratuito
eficiencia OEE
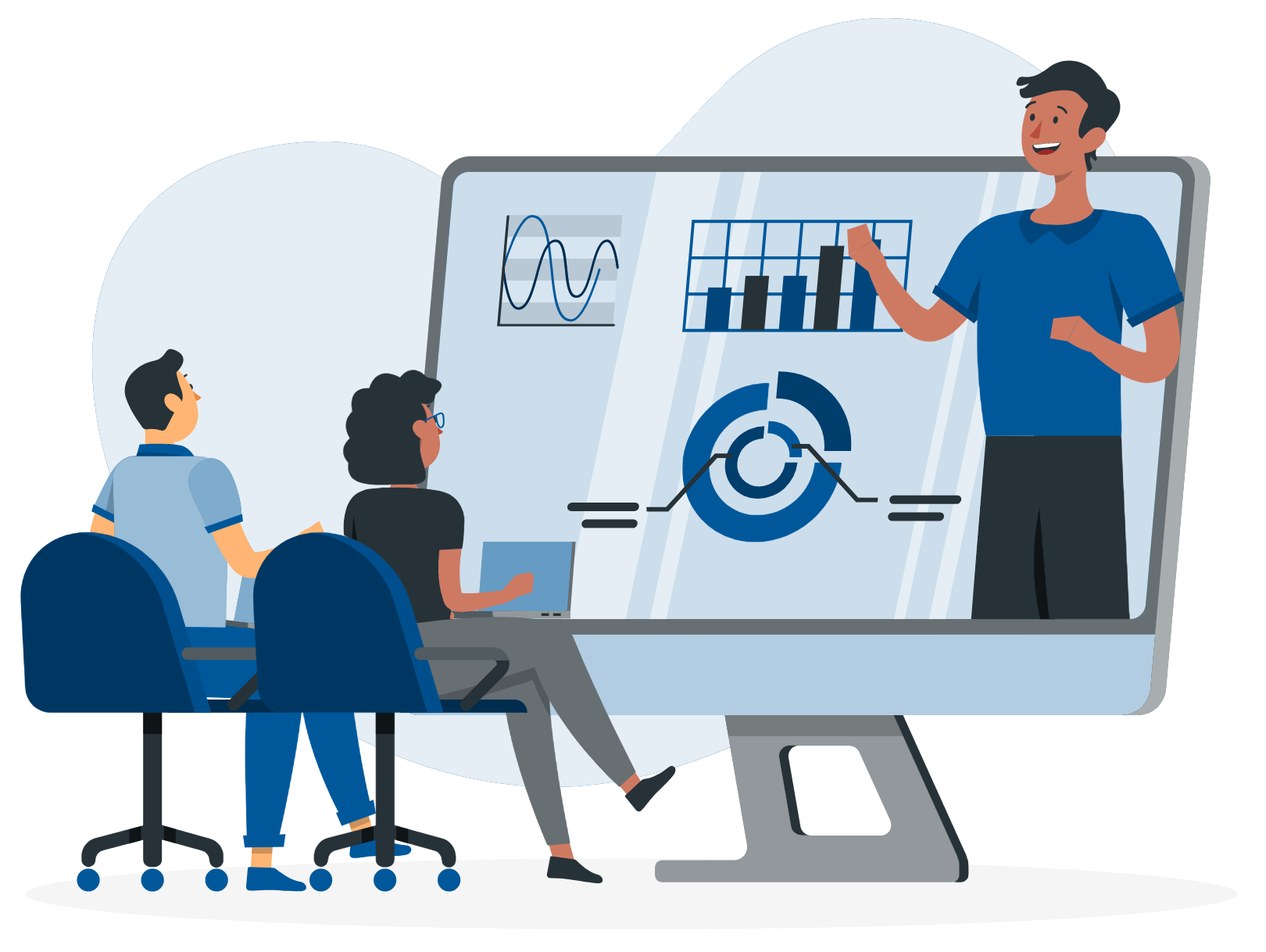
Descubre las particularidades del indicador OEE, cómo automatizar su cálculo y que requisitos deben cumplir tus procesos de producción para implementarlo.