When facing issues related to delays in manufacturing tasks, the main suspects that often emerge are none other than the well-known bottlenecks.
To get an idea of the concept of a bottleneck, we can use a practical culinary example. Let’s move from the industrial environment to our own kitchen and imagine we want to bake several cakes. We only have one oven, the oven’s capacity is one cake at a time, and baking is the operation that takes the most time in the entire process.
Obviously, to bake the second cake, we need the oven to finish with the first one, and so on. Here, we can say that baking is the bottleneck, as it is the slowest operation and, therefore, the one that dictates the pace of baking our cakes.
Taking off our apron and returning to the factory, we define the bottleneck as a slow phase of the production line that slows down the speed of the overall process. It is worth noting that within the same plant and process, we may encounter more than one bottleneck.
In the case of our cake, we could mitigate the effect of the bottleneck by increasing the oven’s power or capacity, but… what can we do in a factory?
What types of bottlenecks exist?
When identifying bottlenecks, we must consider that they can not only occur during the practical application of manufacturing but are also likely to arise in strategic concepts related to the business model.
Within these, we may encounter:
- Lack of business objectives or a clear definition of them.
- Lack of market knowledge.
- Lack of leadership, which negatively impacts worker productivity.
On the other hand, there are bottlenecks directly involved in the production tasks themselves. In this group, there can be many and varied ones, especially due to the peculiarities of each product and the company’s know-how. Still, we can highlight some common ones, such as:
- Those related to labor, either due to its lack, poor management of available human resources, or the lack of training.
- Technological problems that cause machinery to not function properly or to be out of service due to a breakdown.
- Bottlenecks resulting from a lack of stock. No matter how fast we can produce, it is of no use or, even, it can harm us if we do not have sufficient storage and the proper conditions for our products or raw materials.
How to reduce production delays in industry
The first step is to identify the bottlenecks
The best way to identify bottlenecks in our factory will be through monitoring as many operations as possible. However, there will always be some that are more delicate and prone to becoming a bottleneck, so we should pay special attention to these.
Among these “sensitive” operations, we can include the following:
- Those that have a more costly adaptation to high demands, as their low flexibility can slow down the entire chain.
- On the other hand, there are the most critical actions, which, although they have greater flexibility, their stoppage would be extremely serious for the entire plant.
- Finally, we recommend monitoring all processes where direct manual intervention is essential, as the human factor significantly increases the likelihood of errors occurring.
Apply effective techniques and technologies
There are many methodologies that can help us meet the planned schedule for our product. Many of them have been covered previously, but it is worth revisiting them with a focus on the approach of this article.
Not long ago, we talked about the Agile methodology, and more specifically about SAFe and SAM (Sixphere Agile Model). These can greatly help address strategic bottlenecks, as they allow us to specify aspects such as the company’s mission, its future vision, its core, objectives, environment, and what makes it stand out from its competitors.
One of the key aspects of these agile methodologies is that they are a powerful tool for team coordination, helping to tackle delays resulting from poor team management. In this regard, it is also very practical to have a task-assisted planner planner that allows for intelligent and automated task assignment based on real-time data analysis.
To mitigate delays related to the production process itself, maintaining order and cleanliness throughout the production line will facilitate the work of employees and ensure that machinery operates optimally. To ensure that all of this is being followed, we can conduct Housekeeping-5S audits, eliminating anything that does not add value, hinders daily tasks, and/or is a cause of risk for workers.
Within the bottlenecks of the supply chain and, more specifically, those involved in technical failures and management of technological resources or spaces (such as storage), it will be of great help to have a solution that takes care of to plan and manage the plant’s production in a comprehensive manner.
To achieve this, in our case, we have Polaris Industry, which, by integrating proximity technologies, Artificial Intelligence, Machine Learning, Big Data, and IIoT, provides us with complete control over everything happening in our factory, allowing us to always make the best data-driven decisions.
With these types of tools, we will be able to identify existing delays, their causes, the best ways to address them, and even foresee those that are likely to occur, allowing us to treat them proactively.
Maintaining control over the key factors for a plant to operate like clockwork is now much easier thanks to the tremendous technological advancements taking place in these environments. Executives and managers have a wide range of options that will ensure delays become a rare occurrence.
At Sixphere, we offer a range of alternatives to make punctuality one of the hallmarks of your factory. Would you like to learn more about them and see how they could fit into your plant? We are eager to speak with you.
Do you want to know what we do and how we do it? Visit our success stories and ask us anything you need to know.
KNOWLEDGE / Downloadables
Free eBook
OEE Efficiency
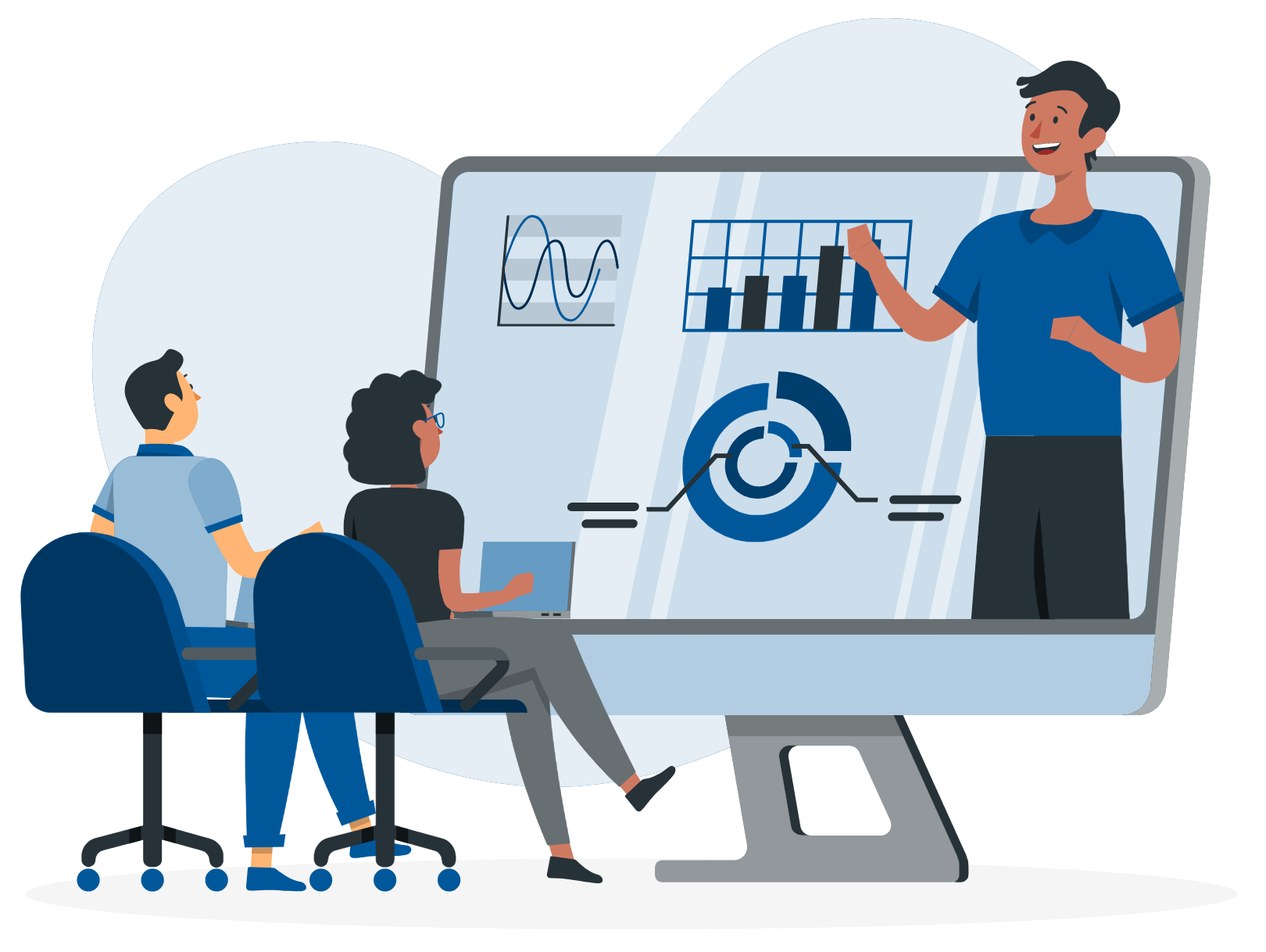
Discover the details of the OEE indicator, how to automate its calculation and the requirements your production processes must meet to implement it.