The word “quality” follows us wherever we go. We only need to turn on the television, the radio, read a newspaper, or visit a website to come across it. Quality is a constant appeal used by brands to promote their products or services. But… do we truly know what it means? Can we define it precisely? This is where many people draw a blank and are unable to provide a clear answer.
And indeed, although we may have a vague idea of the concept of quality and its benefits, it is difficult to fully grasp everything that lies behind this omnipresent word. Moreover, understanding how quality standards are applied to industrial aspects is even more complex.
In this article, we shed more light on quality in the industrial sector—what criteria it follows, how it is implemented, and the advantages it offers to those who commit to it. Want to stand out in your next conversation when the topic of quality comes up? This is your moment to learn more and leave everyone speechless.
What is industrial quality?
Let us begin by clarifying concepts. According to the International Organization for Standardization (ISO), quality is defined as the “degree to which a set of inherent characteristics of an object (product, service, process, person, organization, system, or resource) fulfills requirements.”
These requirements will vary depending on the purpose and the field of application of the concept of quality. For example, the criteria used to assess quality in relation to the environment will not be the same as those used for risk prevention.
The techniques to be used will vary significantly depending on the company’s activity, although the conceptual foundations remain the same: understanding the product’s requirements, verifying that they are met and can be improved, and taking corrective actions when deemed appropriate.
Quality is something that is alive and constantly moving, always seeking continuous improvement. Therefore, the best way to graphically define this pursuit of excellence is through a cycle, known as the Deming Cycle, which consists of the following stages:
- Plan the actions.
- Do the actions.
- Check by measuring the results of those actions.
- Act based on the results obtained in the third stage.
Quality applied to industry encompasses a wide range of fields that may vary depending on the nature of the industry itself. In other words, quality is not the same for a company that manufactures cars as it is for the food industry, although it is true that they may share some common criteria.
Industrial quality standards
As we mentioned, depending on the type of industry, different quality criteria will be applied. However, there are core criteria that are fundamental regardless of the industrial sector we are dealing with.
In order to unify and standardize these quality criteria, various international organizations were established throughout the 20th century to draft these standards. Currently, the main entity for defining quality standards is the ISO, as previously mentioned.
There is a wide range of ISO standards available, and since it would be impractical to discuss all of them in detail, we will refer to some of the most relevant ones for achieving high levels of industrial quality, from a generic perspective to a more specific one depending on the industry itself.
ISO 9001: Starting with the basics
This standard sets the guidelines for establishing a Quality Management System. Its goal is overall customer satisfaction and is independent of the company’s sector of activity. Therefore, when starting to implement quality, it should be the first standard to consider.
The ISO 9001 standard takes into account all processes that impact the overall quality of the business, designing and implementing a system that allows for their management. ISO 9001 addresses aspects such as:
- Context of the organization.
- Leadership.
- Planning.
- Support and management of all necessary resources.
- Operations to be carried out.
- Evaluation.
- Continuous improvement.
ISO 14001: Environment
Currently, industry cannot remain indifferent to environmental issues, which is why following the ISO 14001 standard can be of great interest.
This, like ISO 9001, is a standard with a wide range of applications. In fact, according to AENOR, it is estimated that by 2017, around 362,610 companies in 181 countries held this certification.
The ISO 14001 standard has the general purpose of protecting the environment, achieving this through risk reduction, compliance with current legislation, and establishing strategies for communicating environmental information.
ISO 16949: Automotive Industry
This standard is the one established by ISO for the automotive industry. It sets the requirements for the manufacturing of parts necessary to build a car. It is based on the previously mentioned ISO 9001.
ISO 16949 focuses on preventing the creation of defective parts and reducing the amount of waste generated as a result of this industrial activity.
This standard is extendable to the entire supply chain, as well as to after-sales service and other supporting activities.
EN 9100: Quality in the Aerospace Sector
The standard that specifies the criteria to ensure quality in the aerospace sector focuses its efforts on safety and technology across the entire supply chain. Like ISO 16949, this standard also bases much of its content on ISO 9001.
It has been applied since its inception by prestigious companies in the sector, such as Airbus and Boeing, and is an non-negotiable requirement for all their suppliers. It is important to highlight that the EN 9100 standard is followed both in the civil aviation and military sectors.
Additionally, it is important to note that this standard is applicable to service companies focused on this sector, such as laboratories or organizations responsible for providing technical support.
These are just a few examples of the wide variety of quality standards that exist and can be related to industry. However, they are certainly not the only ones, as several others can be mentioned, such as:
- ISO 15504 for software development.
- ISO 20000 for IT services.
- ISO 50001 for energy management.
- ISO 27001 for information security.
Implementation of a quality management system
Up to this point, we have covered the more theoretical aspects of industrial quality. Now, it’s time to move to the practical side and briefly analyze how a quality management system is implemented in an industry. A common way to do this is through the following steps:
- Situation diagnosis. Before starting, we need to know where we stand. To do this, reports, records can be analyzed, surveys or interviews conducted, and relevant legislation checked. Detailed monitoring of all processes is also important in this phase, as well as performing a SWOT analysis (DAFO).
- Drafting the necessary documentation, such as the policy, the plan, and the quality manual, as well as the various work procedures.
- Training and awareness tasks to ensure employee involvement.
- Implementation of the quality system. Time to get started.
- Internal audit. These will be repeated at regular intervals.
- Application of corrective, preventive, and improvement actions based on the results of the internal audit.
- External audit. If it is favorable, we will obtain the desired quality certification.
Logically, we could go into more detail on each of these steps and even break them down further, but we understand that this is not the purpose of this article. Therefore, we have chosen to provide a brief overview of the procedure.
To have complete control over this process, we can turn to technological solutions that facilitate the management of industrial quality. One such solution is Polaris Industry, which makes it easy to monitor every action taking place in the factory using proximity technologies and Artificial Intelligence.
Advantages of industrial quality
Why is quality so important in industry? Naturally, putting so much effort into establishing a quality system for our company should provide considerable benefits. Otherwise, such an effort would not be worthwhile. Let’s take a look at the most notable advantages.
Greater customer satisfaction
After all, the end user should be the center of all our actions and, therefore, the driving force that motivates us to strengthen quality in the industry.
There is no better ambassador for your brand than a satisfied customer with what we offer. They will return to us and recommend us to everyone around them. But that’s not all; the reduction of complaints and claims allows us to allocate more resources to other tasks.
Cost reduction
The implementation of a quality system results in lower production costs. This is because materials are used more efficiently, reducing waste of raw materials, semi-finished products, and finished goods.
The optimization of work processes promotes large-scale production, which lowers manufacturing costs. Additionally, savings are made in investments aimed at monitoring and correcting errors.
Motivated employees
When everyone involved in the processes realizes that, thanks to their effort and dedication, everything runs smoothly, their morale will skyrocket. This will lead to lower employee turnover, meaning we’ll have experienced workers who are eager to continue growing.
But that’s not all; having motivated staff ensures that the relationship between them is optimal, creating a great work environment.
Higher sales
The higher the quality standards, the better products we will create, which will have a direct impact on sales figures. Additionally, by having greater control over everything happening on the production floor, we can be more accurate when setting prices for our products. Therefore, we have the opportunity to establish a quality-price ratio that is highly attractive to the public.
We hope that after reading this article, the concept of quality and why it is so important to apply it across all areas of industry is clearer to you. It won’t be easy or quick, but it’s worth rolling up your sleeves and getting to work, all together and in a coordinated manner. Additionally, with the help of tools offered by new technologies, everything will be easier and more reliable. Let’s go for it!
Do you want to know what we do and how we do it? Visit our success stories and ask us anything you need to know.
KNOWLEDGE / Downloadables
Free eBook
OEE Efficiency
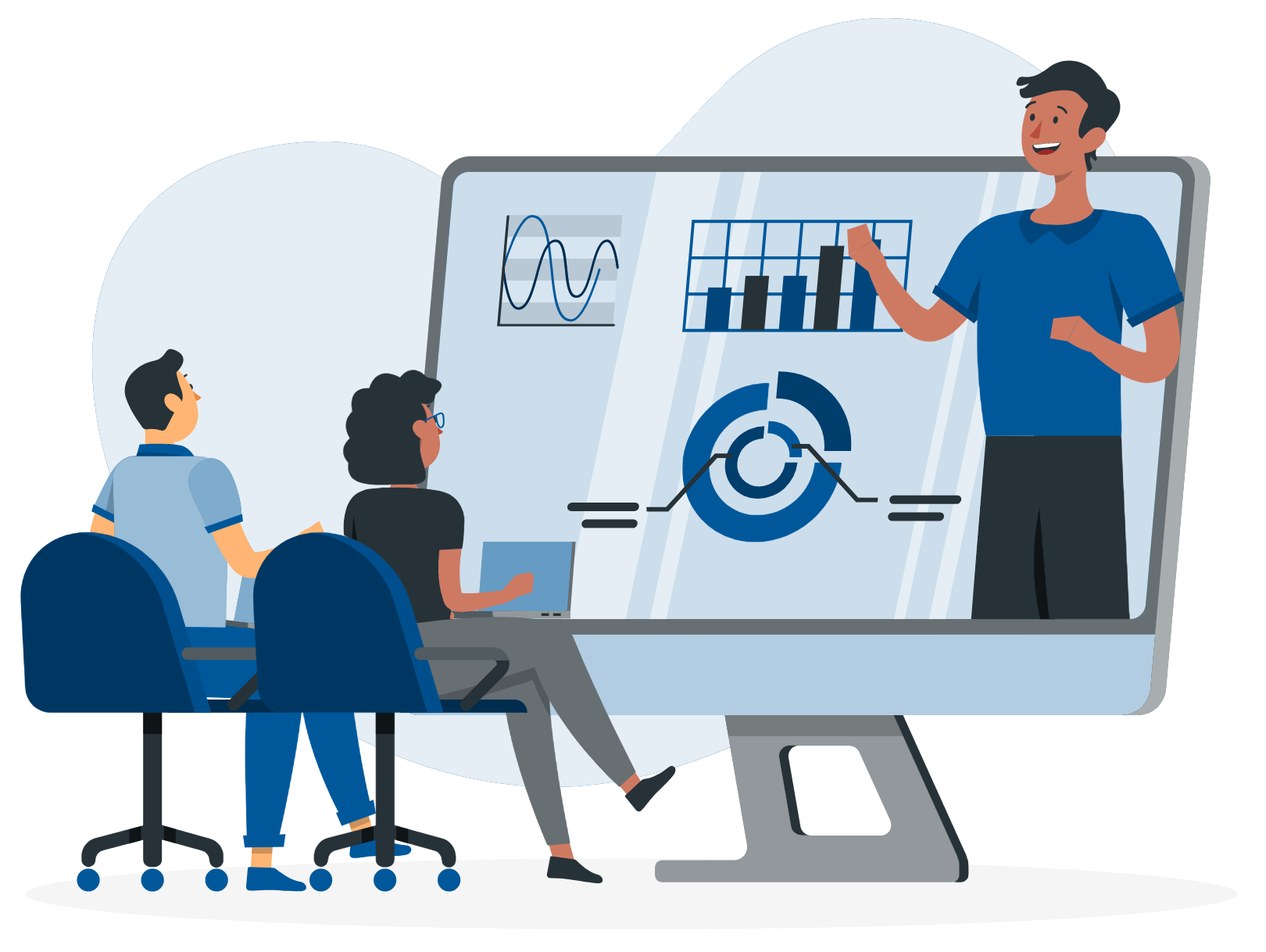
Discover the details of the OEE indicator, how to automate its calculation and the requirements your production processes must meet to implement it.